For those in the food packaging sector, the importance of maintaining product integrity and quality cannot be overstated. A leading multinational food and drink manufacturing conglomerate has dramatically improved its leak detection processes by upgrading from traditional bubble leak testing to the advanced vacuum decay testing provided by Oxipack.
.jpeg)
Known for its commitment to excellence, this company consistently seeks innovative solutions to enhance product safety and consumer satisfaction. The initiative to improve their packaging leak detection systems was driven by an urgent need to address persistent issues affecting packaging integrity, crucial for maintaining product quality and strengthening consumer trust.
Understanding the challenge
“We had been experiencing persistent challenges with pouches leaking, and despite rigorous testing through burst tests, wring tests and water bath or bubble leak testing, were still not able to sufficiently identify the leakers. It is why we explored the availability of other tests, and found the vacuum leak detection solution from Oxipack.”
The move was triggered following the company using an advanced investigation tool to identify why leaking pouches became a recurring issue. The investigation focused on understanding the reason for the defects. To this end, it was decided that the company needed to adopt a different testing solution to identify leaks in real-time. It wanted to reduce its defect rates and resultant consumer complaints.
Previously reliant on conventional bubble leak testing, the company faced significant challenges using this method. It was not only labour-intensive but also less effective at detecting minor, yet critical, leaks. This inefficiency saw the organisation embark on a search for a more reliable and effective solution.
Selecting Oxipack
“While our investigation was not about finding a new tool, but rather about understanding why we were seeing defects. Through rigorous testing and investigation, we understood we needed a better tool to enable us to find leaks in real time, to improve defect rates and address consumer complaints we may have had.”
The company’s search for an improved leak detection solution emphasised the need for robustness, accuracy, efficiency, and dependability. Oxipack’s vacuum decay method, which detects leaks through precise pressure change measurements within sealed packages, proved to be superior to competitor offerings. Early testing phases showed exceptional results, with the technology successfully identifying all leaks without any false positives, ensuring the integrity of each product on the line.
After choosing Oxipack's solution, extensive validation tests were conducted during 2014 and 2015 that demonstrated the system's effectiveness and operational benefits. In 2016, the implementation of Oxipack’s technology on their production lines began. This testing replaced the outdated methods as a primary solution to significantly streamline the leak detection process while keeping bubble testing as a backup process. Training was provided to operators, facilitating a seamless integration into the existing production environment.
“Undoubtedly one of the biggest challenges is getting the operators to buy-into the new system. We decided on a progressive implementation with Oxipack, focusing first on identifying and resolving the main leak points, validating the results and in so doing building the confidence of the operators.”
The results
The adoption of vacuum decay testing yielded significant improvements. The new method drastically reduced wastage and increased detection accuracy. Its real-time detection capabilities allowed for immediate problem-solving, significantly reducing the risk of quality issues reaching consumers. This change led to a 60% decrease in incubation test failures, enhancing both production uptime and overall quality control.
Testimonials received highlight the robustness and user-friendliness of Oxipack’s technology as key to its successful integration. The ability to simultaneously test eight pouches and receive instant results has greatly improved operational efficiency and employee satisfaction.
“In particular, the Oxipack Detector has given us the ability to find faults in real-time, giving our engineers the opportunity to troubleshoot quickly, without compromising on quality and production time. We see this as a great business advantage.”
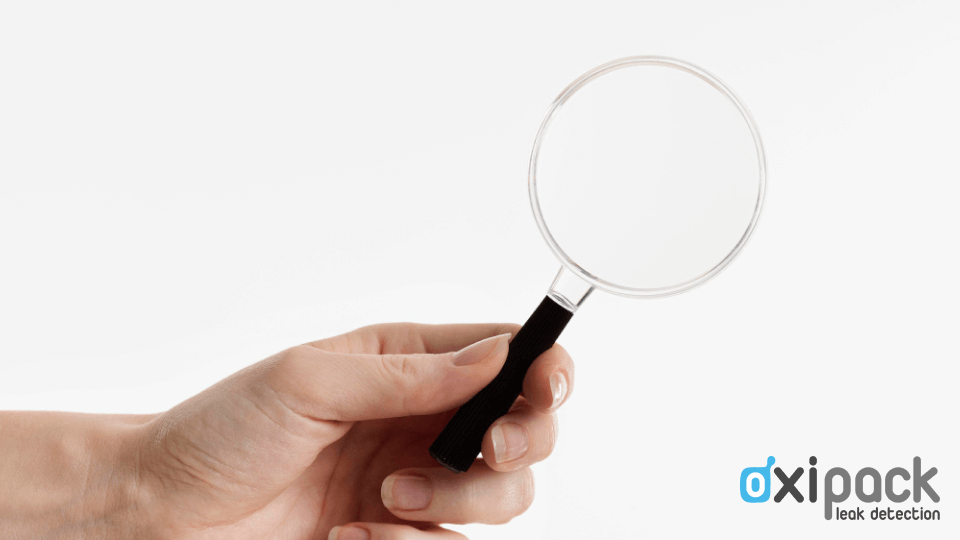
For businesses in the food and pharmaceutical sectors aiming to boost their packaging integrity and operational efficiency, Oxipack’s vacuum decay testing offers a groundbreaking solution. We encourage you to consider how Oxipack can strengthen your quality assurance processes and redefine industry standards.
For more information and to connect with our team, please visit the Oxipack website.