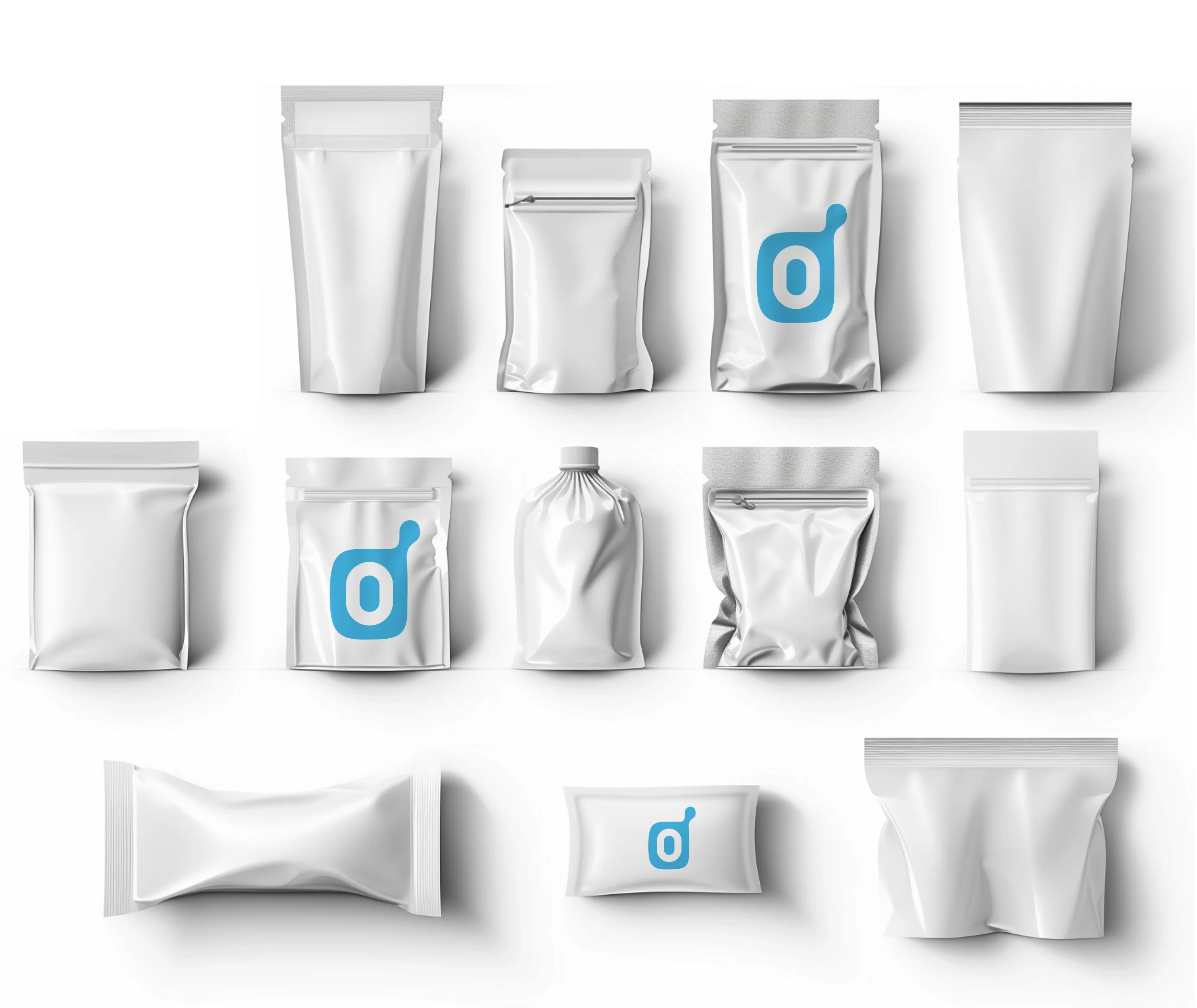
Testing Flexible Packaging For Leaks
At Oxipack, we're setting new benchmarks in leak detection for flexible packaging. Our advanced, non-destructive technology preserves product integrity and reduces operational costs, ideal for the pharmaceutical, food processing and pet food industries.
why Flexible packaging?
Flexible packaging offers exceptional versatility and efficiency, reducing material use and allowing for innovative design options that enhance product appeal and functionality. Our leak testing solutions ensure that this type of packaging remains airtight and secure, protecting contents from contamination and extending shelf life.
The Stationary Leak Tester is versatile, easily testing various products like pet food, chocolate, and milk powder with just one set of parameters.
Oxipack's leak detection technology incorporates multivariate measurement capabilities, enabling simultaneous analysis of multiple factors affecting package integrity. This comprehensive approach allows for more nuanced assessments, detecting a variety of potential issues in real-time, thus ensuring a higher standard of packaging quality and consistency across production batches.
Operators can easily manage our leak detection machines with minimal training, thanks to intuitive controls and clear, immediate feedback on the testing status via visual indicators.
Modified atmospheric packaging (MAP), and flexible packaging without any inert gases or even little air inside can be tested non-detructively.
When testing multiple items, if a leak is detected, the Stationary Leak Tester promptly indicates its presence.
Built to last, our leak testers are developed to withstand the rigors of industrial environments, ensuring reliability and durability in high-demand scenarios.
The measuring cycle completes within thirty seconds, detecting leaks as small as 10 µm.
The equipment complies with the Standard Test Method for Non-destructive Detection of Leaks in Packages by Vacuum Decay Method (ASTM F2338).
The Importance of Non-Destructive Leak Testing for Flexible Packaging
Non-destructive leak testing for flexible packaging plays a key role in maintaining product safety and quality by ensuring that packaging integrity remains intact throughout the supply chain. This method boosts consumer trust and significantly cuts waste and operational costs, as it allows for immediate corrections without the need to destroy the packaging.
Frequently Asked Questions
With non-destructive leak detection, you can achieve considerable savings. Leaking packages cause losses across the entire chain and could inflict significant damage to a brand’s image. Each factory is unique and savings are relative to the circumstances, the product and the raw materials used. Non-destructive leak testing allows for even bigger savings: all approved products can go back in the production line. You can imagine our machines have recouped themselves within a couple of months.
Your current percentage needs to be established first. Accurate analysis of the actual leakage percentage is key for chain optimisation.
The number of leaking packages produced can be tricky to pin down. In-depth research often demonstrates that the leakage percentage is much higher than originally estimated. Then there are all manner of considerations and invested interests at play and of course views on leak detection may differ. No one wants to halt a production line, however this may result in large numbers of packages having to be destroyed further down the chain.
Focus on the source: the packaging machine. Once it is known how many leaking packages it produces, you can have the machine, and therefore the leakage percentage, rapidly under control. Systemic leaks can be detected by methodical spot checking. Random leaks can only be traced by a 100% leak detection system.
Each Leak Tester, reduces the space surrounding the packaging to a minimum. This is done using flexible membranes and/or moulds mirroring the form of the product and leaving as little space as possible between this and the product. The space between the rubber form/mould and the actual packaging is subjected to a vacuum. The equipment measures the precise air pressure and then repeats this seconds later. If there is a change in pressure between the two measurements, then there is a leak. Even though pressure sounds rough, no stress is put on the package or the product itself. The membranes embrace the product so gently that when the pack is OK, not even a potato crisp is cracked.
The Oxipack leak testing equipment can detect very small perforations in vacuum packaging and soft packages down to 10 micron (µm). That’s one-hundredth of a millimeter. This places the equipment as the most accurate non-destructive micro leak testing equipment available to the packaging industry. It allows you to check that your lines are packaging products as airtight and leak-proof as possible, preventing complaints and quality issues through deterioration.
The complete leak test is finalised within about 30 seconds. Testing a small product package will be a couple of seconds faster than testing relatively larger packages.
Of course! We have several rental leak detection equipment ready for shipment! And our special crates will make sure the Leak Tester(s) arrives in perfect condition. Getting started is easy: just put the plug in the power socket and connect compressed air. You can now turn on your leak tester and start testing for leaks.
Operation is simple, place the package inside and within approximately 30 seconds the machine will indicate whether the package is airtight. This will give you a rapid and accurate reading of the packaging performance of a particular packaging line.
Our Packaging Methods
Explore our other packaging methods.
Insights
Explore our latest News, Blogs, Cases and Whitepapers
Can My Flexible Packaging Be Tested?
Are you looking to make a lasting impact on your business? Eliminate the potential loss of quality, time, and money by choosing Oxipack for advanced leak detection in your packaging. Click below to request a consultation and discover how our solutions can be tailored to meet your specific packaging needs.
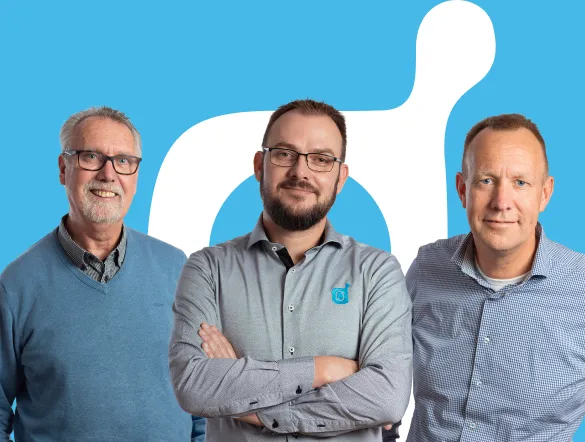