.webp)
Testing Bottles And Caps For Leaks
Advanced leak testing ensures every bottle & cap seals perfectly, safeguarding liquids and meeting top quality standards.
Bottles Must Be Airtight
Bottles and caps are fundamental in maintaining the quality and safety of liquid products, from beverages to chemical solutions. Our precise leak testing procedures ensure that every bottle and cap combination is rigorously evaluated to prevent contamination and leakage, upholding the highest standards of packaging integrity.
Oxipack’s systems specialize in ensuring the tightness and proper sealing of bottle caps, crucial for preventing contamination and maintaining product quality throughout shelf life.
Our technology supports a broad range of bottle shapes, sizes, and materials—from glass to plastic—ensuring flexible application across various sectors, including beverages, pharmaceuticals, and personal care products.
Bottles are positioned in a chamber where a vacuum is applied, exposing them to negative pressure. If there are any leaks, air or gas escapes. While detection is often facilitated by a custom FDA-approved membrane, we also have the capability to test bottles without a membrane, depending on the specific requirement of the test.
Simple to operate, our leak detectors provide instant feedback via an intuitive interface, with clear indicators for pass/fail results, empowering operators to make quick decisions on the production line.
Designed for efficiency, our detection systems swiftly identify leaks without slowing down the production line, enabling high throughput and minimizing disruption in fast-paced manufacturing environments.
With advanced sensors, our machines precisely measure pressure differences to detect even the smallest leaks at the cap or bottle interface, providing a critical quality check before products reach consumers.
Fully automated testing capabilities allow for the assessment of large volumes of bottles and caps, making our technology ideal for extensive production runs that require consistent quality assurance.
Our equipment meets stringent industry standards, ensuring that all testing procedures for bottles and caps comply with international regulatory requirements, which helps safeguard brand reputation and consumer trust.
The Importance of a Non-Destructive Leak Test for Bottles And Caps
Non-destructive leak testing safeguards both product quality and consumer safety for bottles and caps. This method ensures effective seals and prevents contamination, all without damaging the product. Every unit undergoes a thorough inspection, guaranteeing it meets stringent quality standards before reaching your hands.
Frequently Asked Questions
The answer is yes 90% of the time. Let us know what you need and we will run some tests to see what the possibilities are.
Yes, as long as there is enough headspace.
When we receive your photos and samples our Centre of Expertise will examine the possibilities and propose a test method tailor-made for your challenge.
There is an R&D/laboratory version of this leak tester available. With a touch-screen and easy to operate menu, you can perform the tests on leak-tightness yourself.
Our Projects team will gladly take a look for automated quality control systems fitting your packaging! Send us your requirements together with pictures of the products you would like to test and we will have an answer for you within two weeks.
Our Packaging Methods
Explore our other packaging methods.
Insights
Explore our latest News, Blogs, Cases and Whitepapers
Can my bottles and caps be tested?
Are you ready to make a lifelong impact in your business today? Stop wasting quality, time and money. Instead, choose Oxipack for detecting leaks in your packaging! Click below to request advice and see how our equipment can match your packaging specifications.
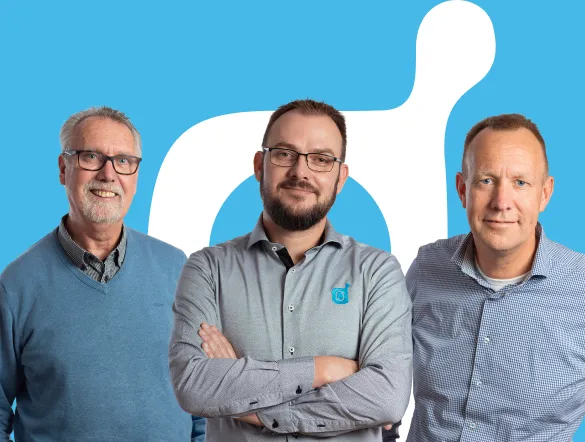