Understanding Leak Detection
Key Leak Detection Methods:
Leak detection technology has come a long way, providing reliable and innovative solutions for various packaging types and production setups. Here are some of the most effective and widely used methods:
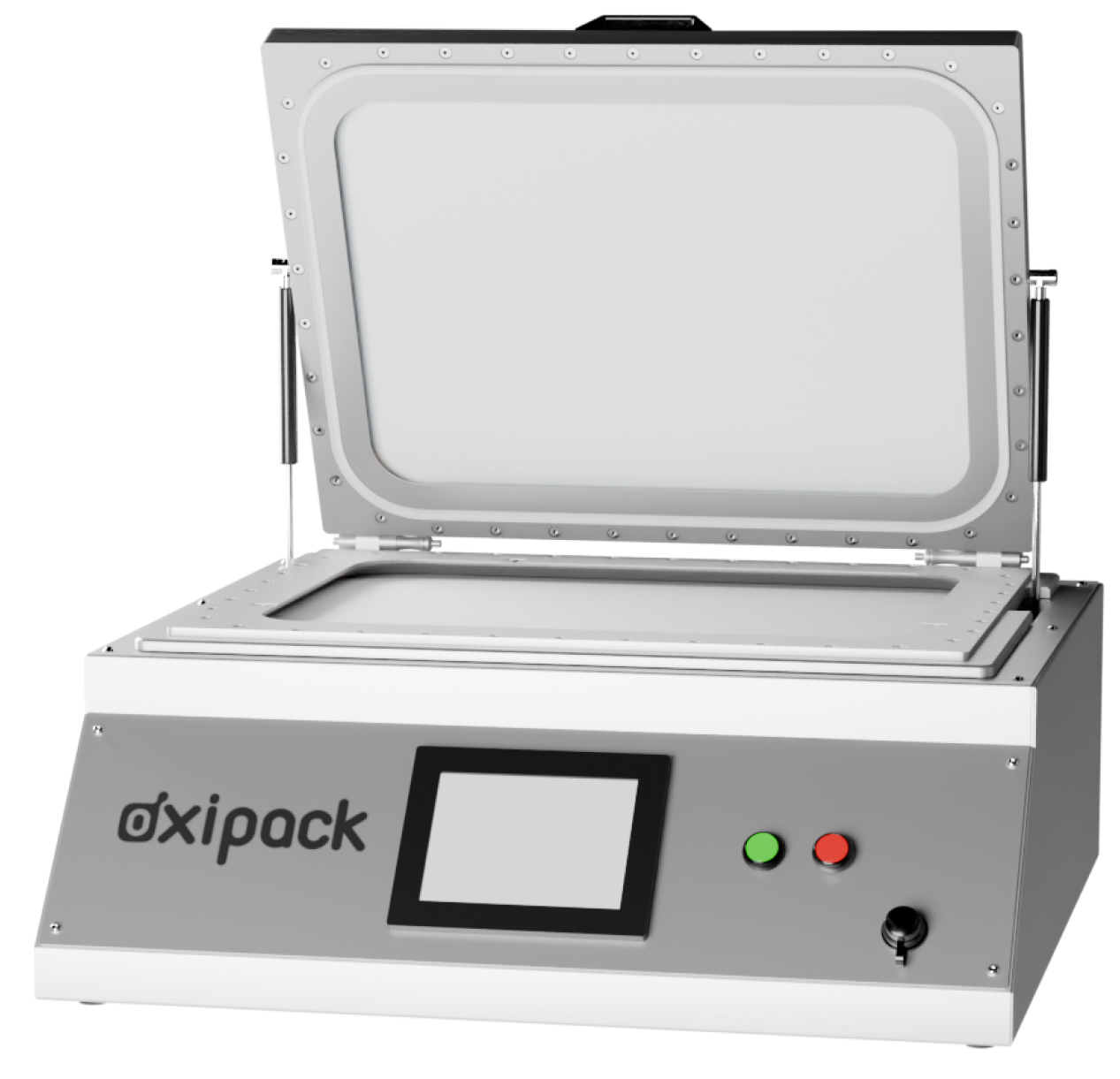
Vacuum Decay Testing
One of the most sensitive and non-destructive methods, vacuum decay testing measures pressure changes in a test chamber to detect leaks. It’s ideal for high-risk products where precision is key. This method aligns with ASTM standards and is widely used for detecting micro-leaks in flexible and rigid packaging.
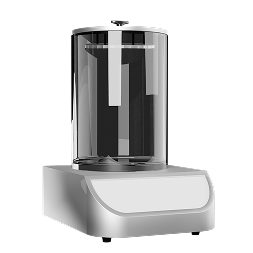
Bubble Emission Testing
A simple yet effective method, bubble emission testing involves submerging the package in water and applying pressure or vacuum to observe if air bubbles escape. While cost-effective, it is destructive and less sensitive than other methods, making it best suited for larger leak detection.
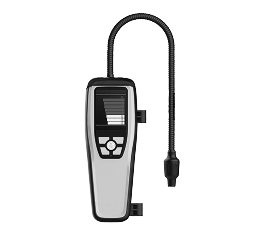
Tracer Gas Detection
Using gases like helium or carbon dioxide, this method fills packaging with the tracer gas and measures for leaks using sensitive gas detectors. Tracer gas detection is one of the most precise techniques, ideal for detecting the smallest leaks, but it requires specialized equipment.
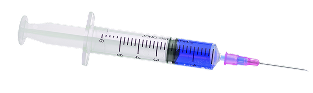
Blue Dye Testing
Blue dye leak testing is a probabilistic, destructive method used to detect leaks in sealed packages. The package is submerged in a blue dye solution, and any leaks are identified by the presence of dye penetration, though it is prone to false positives and lacks quantitative accuracy.
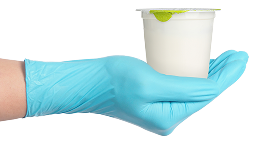
Manual Leak Test
Manual leak testing is a subjective and non-standardized method where an operator physically squeezes a package to check for escaping air or product, indicating a leak. This method is highly inconsistent, relies on human perception, and cannot detect microleaks reliably.
Choosing the Right Leak Detection Strategy:
Choosing the right leak detection method depends on your packaging and production setup. Keep these key factors in mind when deciding on the best approach:
Different methods work better for flexible packaging (e.g., pouches) versus rigid packaging (e.g., bottles or trays).
High-risk products or sensitive packaging environments may require more precise methods like vacuum decay or tracer gas detection.
For high-throughput environments, methods like ultrasonic detection offer fast, non-invasive testing.
Non-destructive methods like vacuum decay allow packages to remain intact for further testing or sale.
Ensure your testing method complies with industry standards, such as ASTM F2338 for vacuum decay, to meet regulatory expectations.
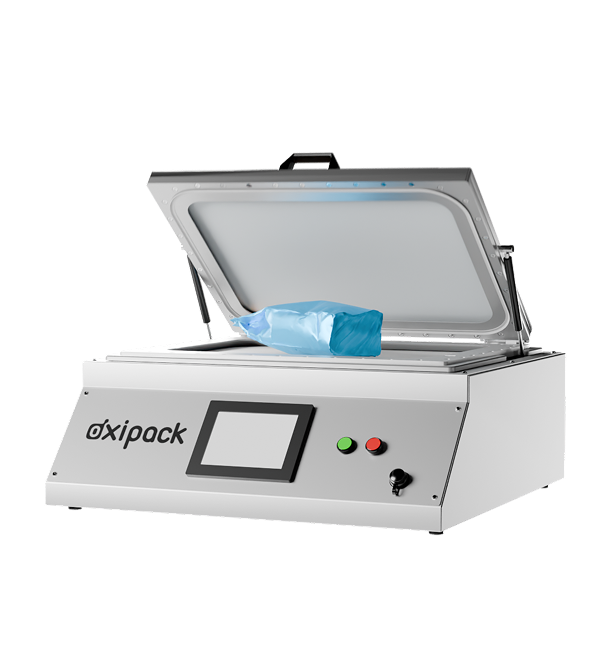
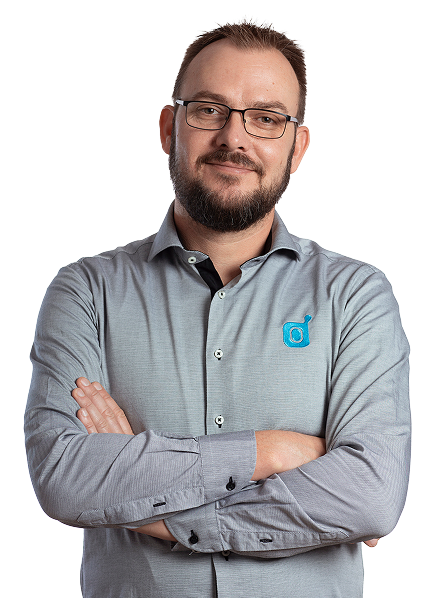
Best Practices for Leak Detection:
Having the right equipment is only part of the equation when it comes to leak detection. To get accurate and reliable results, you also need solid operational practices. Here are some key ways to improve your process:
Take the Next Step in Production Excellence
Ready to elevate your production line with state-of-the-art in-line testing solutions? Contact Oxipack today to find out how our technologies can be integrated into your manufacturing processes to ensure every product is perfect.
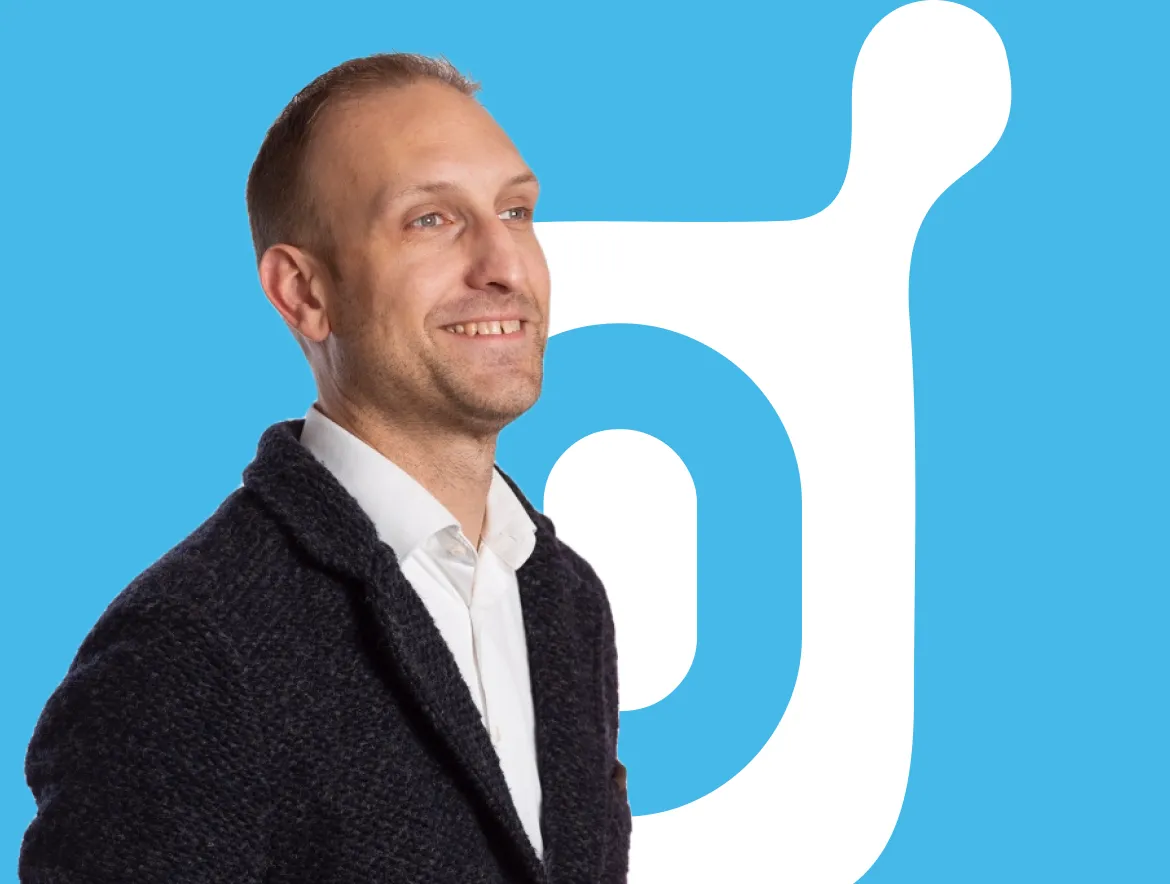