What is Vacuum Decay?
Is your packaging truly leak-proof? Vacuum decay testing is the gold-standard method for uncovering hidden leaks, ensuring your products stay fresh, safe, and high-quality—all without damaging a single package.
Everything You Need to Know About Vacuum Decay:
Vacuum Cycle Curve
How Does Vacuum Decay Work?
Preparation
The sealed package is placed inside a test chamber, and the chamber is sealed.
Vacuum Application
A vacuum is applied to the chamber, reducing the internal pressure.
Monitoring
The pressure inside the chamber is monitored over a set time period. If there is a leak, air will be drawn into the package, causing a rise in pressure.
Analysis
The system analyzes the pressure change to determine if the package is airtight or has a leak.
Benefits of Vacuum Decay Testing:
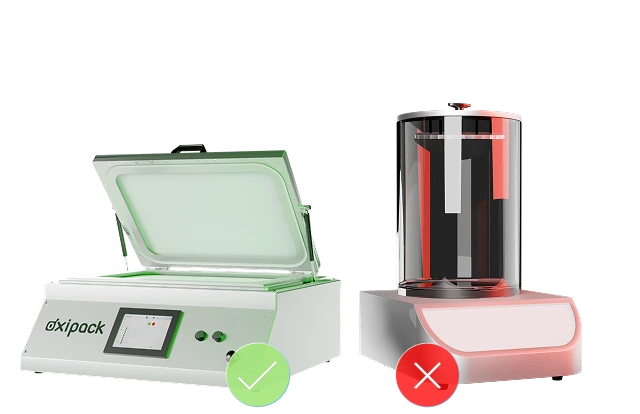
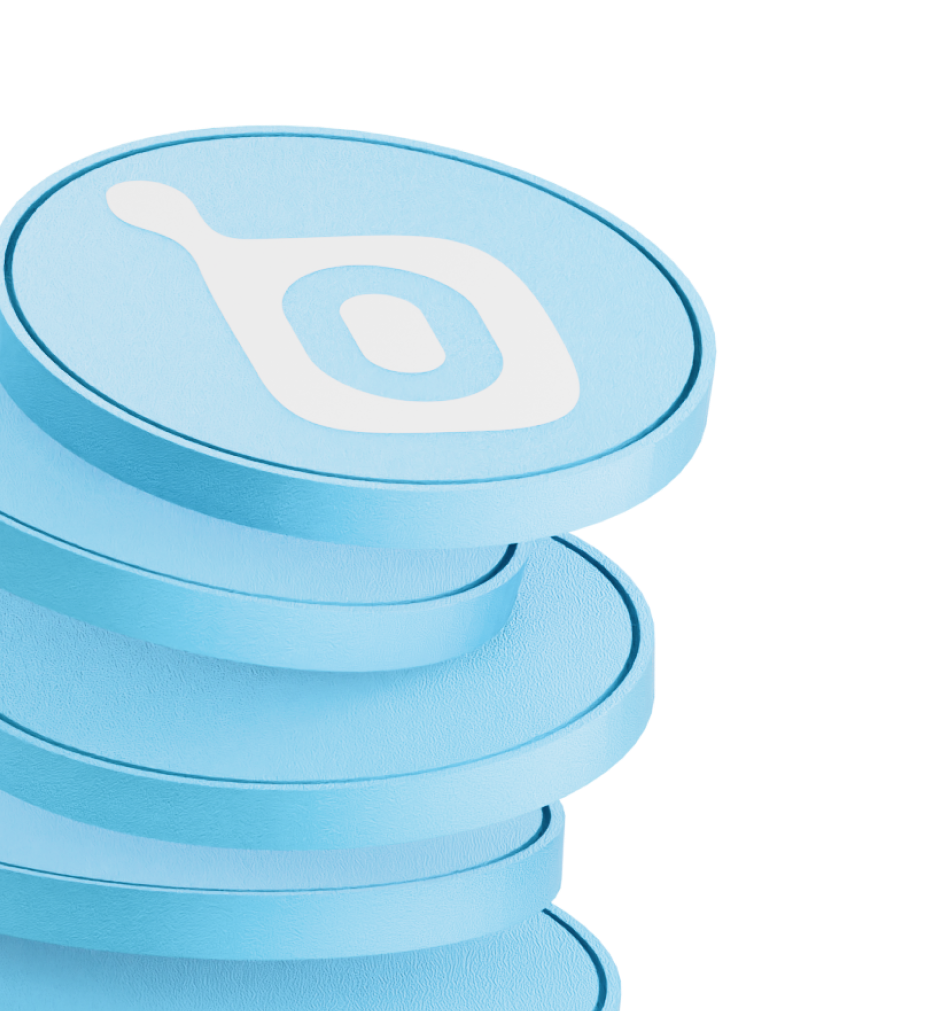
When Should You Use Vacuum Decay Testing?
%201.png)
Best Practices for Vacuum Decay Testing
Ensure proper Verification and Validation of the vacuum decay system for accurate results.
Regularly inspect the test chamber and seals to avoid false positives.
Set the appropriate test parameters (vacuum level, test duration) based on packaging type.
Maintain detailed documentation for regulatory compliance and quality assurance audits.