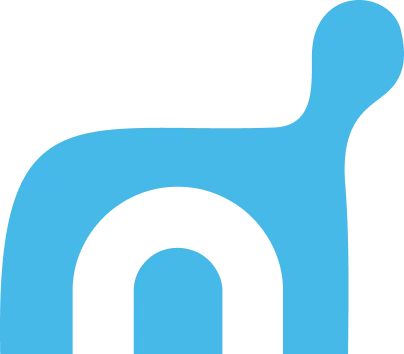
General FAQ’s
How does Oxipack contribute to maintaining Acceptable Quality Levels (AQL)?
The Acceptable Quality Level (AQL) is a critical benchmark in quality control that defines the maximum number of defective items considered acceptable during random sampling. Oxipack's leak detection systems are engineered to deliver high-precision testing, helping manufacturers maintain AQL standards by swiftly identifying and rejecting packages with leaks, thereby ensuring product integrity and consumer safety.
What is ASTM F2338 and why is it important for a leaktest?
ASTM F2338 is a standard method for conducting leak checks in packaging through vacuum decay, playing a crucial role in leak testing. It offers a non-destructive, sensitive, and reliable approach to ensure packaging integrity. Oxipack's leak detection solutions, designed in accordance with this standard, guarantee precision and the ability to detect even the smallest pressure differences in packaging.
What defines a leak? And how do we know if our packaging is leaking?
A leak is defined as any unintended opening in packaging that allows the contents to escape or external substances to enter. To determine if your packaging is leaking, we use sophisticated leak detection methods, such as vacuum decay testing, which can detect even the smallest pressure differences indicating a breach in packaging integrity. This method provides a reliable way to ensure your packaging is secure and leak-free.
How can I get a demo of Oxipack’s leak detection machines?
Getting a demo of Oxipack's leak detection machines is simple! Just reach out to us, and we'll schedule a demo at your convenience. Our team is excited to demonstrate the capabilities of our cutting-edge technology and answer any questions you may have. Contact us today to arrange your demo!
How can I purchase an Oxipack leak detection machine?
To purchase an Oxipack leak detection machine, simply reach out to us through our website, email, or phone. Our dedicated team will assist you every step of the way, from understanding your unique requirements to selecting the right machine and discussing customization options and pricing. We're here to ensure that you find the perfect solution for your leak detection needs.
How accurate are Oxipack’s leak detection machines?
Our leak detection machines are extremely accurate, capable of performing a thorough leak check and identifying even the smallest leaks (>0.9 cm³/min for some models) within seconds. This ensures the highest level of quality control for your packaging through precise leakage tests.
Are Oxipack's leak detection methods safe for all types of products?
Absolutely. Our non-destructive leak detector methods ensure that the product inside the packaging remains untouched and uncontaminated, making it safe for food, pharmaceuticals, and other sensitive products. Our non-destructive leak detection methos is based on vacuum decay ASTM F2338 standard. You can read more here: https://www.oxipack.com/insights/a-guide-to-testing-methods-how-astm-standards-ensure-package-reliability.
How does the food packaging industry maintain product freshness and safety through leak detection methods?
Leak detection techniques such as vacuum decay and bubble tests are instrumental in ensuring the integrity of food packaging. Utilizing specialized leak detectors, manufacturers conduct leak checks and leakage tests to prevent contamination and maintain acceptable quality levels, thereby safeguarding product freshness and safety.
Can Oxipack's leak detector solutions detect leaks in packaging of any size or shape?
Absolutely! Oxipack's leak detection solutions are designed to detect leaks in packaging of any size or shape. Whether you have small or large packages, irregular shapes, or unique designs, our advanced technology can effectively identify leaks. If you're unsure whether our solutions are suitable for your specific packaging type, don't hesitate to contact us. We're eager to discuss your needs and tailor a solution to ensure your packaging remains leak-proof and secure. Let's start the conversation about how we can assist you with leak detection!
What makes Oxipack’s leak detection methods unique?
Unlike traditional methods that may use bubble tests, or traceable gases, Oxipack's exclusive testing system detects the smallest pressure differences without damaging the packaging. This approach is clean, dry, and highly precise. Oxipack's non-destructive leak detection method is based on vacuum decay ASTM F2338 standard. You can read more here: https://www.oxipack.com/insights/a-guide-to-testing-methods-how-astm-standards-ensure-package-reliability.
What methods are employed for a leaktest in pharmaceutical packaging, and how do they contribute to ensuring product safety?
Leak detection methods such as vacuum decay and bubble tests are widely utilized in pharmaceutical packaging. By conducting thorough leak tests, manufacturers can ensure container closure integrity testing, thereby safeguarding product safety. These techniques, facilitated by leak detectors, play a crucial role in maintaining the required quality standards and preventing potential product contamination or loss.
How does the pharmaceutical packaging industry ensure the integrity of container closures to meet the acceptable quality level (AQL)?
The pharmaceutical packaging industry relies on various methods such as leak detection, including vacuum decay and bubble tests, to conduct container closure integrity testing. These techniques, facilitated by specialized leak detectors, help maintain an acceptable quality level by swiftly identifying any leaks or flaws in the packaging seals through leak checks and leakage tests.
What methods are commonly employed in pharmaceutical packaging quality control to ensure the integrity of sealed containers?
Container closure integrity testing, also known as pharmaceutical package testing, is a crucial aspect of ensuring the quality and safety of pharmaceutical packaging. It involves using quality inspection tools to assess the integrity of sealed containers.
One common method is vacuum decay testing, where the sealed container is subjected to a vacuum to detect any leaks or breaches in its integrity. This process helps pharmaceutical companies maintain the quality and efficacy of their products by ensuring that they are properly sealed and protected.
How can I ensure the integrity of our sealed packages within our production environment?
Maintaining the integrity of sealed packages is critical to uphold quality standards and prevent product loss. One effective solution utilized across industries is vacuum decay testing. This method, facilitated by specialized leak detection machines, provides accurate and reliable results. By subjecting sealed packages to a vacuum environment, we can precisely detect any leaks through monitoring pressure changes. Our comprehensive leak test procedure ensures that even the smallest leaks in package seals are identified. With our expertise and state-of-the-art leak test equipment, including vacuum chambers and pressure sensors, we offer a seamless integration of leakage testing into your production process. This ensures that your products remain secure and intact, meeting stringent quality requirements.
Whether you're in pharmaceuticals, food packaging, or any other industry requiring meticulous quality control, our vacuum decay testing solutions provide the assurance you need to safeguard your products to an acceptable quality level.
What is vacuum decay, and how does Oxipack utilize this method in leak detection?
Oxipack specializes in providing vacuum decay leak testers, employing a non-destructive method for detecting leaks in packaging. Vacuum decay involves measuring the change in pressure within a sealed chamber over time, which serves as an indicator of any leaks present in the packaging. Our range of leak detection machines utilizes this advanced technique, offering clean, dry, and highly precise leak tests without the need for traditional methods such as a bubble test or a trace gas.
What is a bubble test and how does it work?
A bubble test, also known as bubble emission testing or bubble leak testing, is a method used in the packaging industry to evaluate the integrity of sealed packages. This process involves submerging the package in water or a solution and observing for the formation of bubbles, indicating the presence of leaks. While a bubble test is relatively simple and cost-effective, one major downside is its limited sensitivity, as it may not detect very small leaks or those occurring in certain types of packaging materials. It also destroys your products, leading to product wastage. While effective for many applications, it may not be suitable for detecting all potential leaks, and maintaining an acceptable quality level.
What are the different types of seal integrity test methods used in the packaging industry?
Seal integrity testing methods are split into two main types: deterministic and probabilistic. Deterministic methods, like the Vacuum Decay Test and Ultrasonic Testing, provide direct, reliable measurements for checking seal quality. On the other hand, probabilistic methods, such as the Visual Inspection and Bubble Test, depend on chance to assess seal quality, which can introduce some uncertainty and requires interpretation.
What method complies with vacuum decay, and what does it entail for the evaluation of packaging?
The method that complies with vacuum decay for the evaluation of packaging is ASTM F2338.
This standard utilizes the vacuum decay method to nondestructively do a leak test in packages.
Vacuum decay entails subjecting the package to a vacuum and monitoring pressure changes within the package to detect any leaks, basically doing a leak check.
This method allows for the evaluation of various types of packaging, including rigid and semi-rigid non-lidded trays, rigid nonporous packages, and flexible nonporous packages. By employing vacuum decay, ASTM F2338 ensures thorough evaluation of packaging integrity while maintaining the integrity of the package itself during testing.