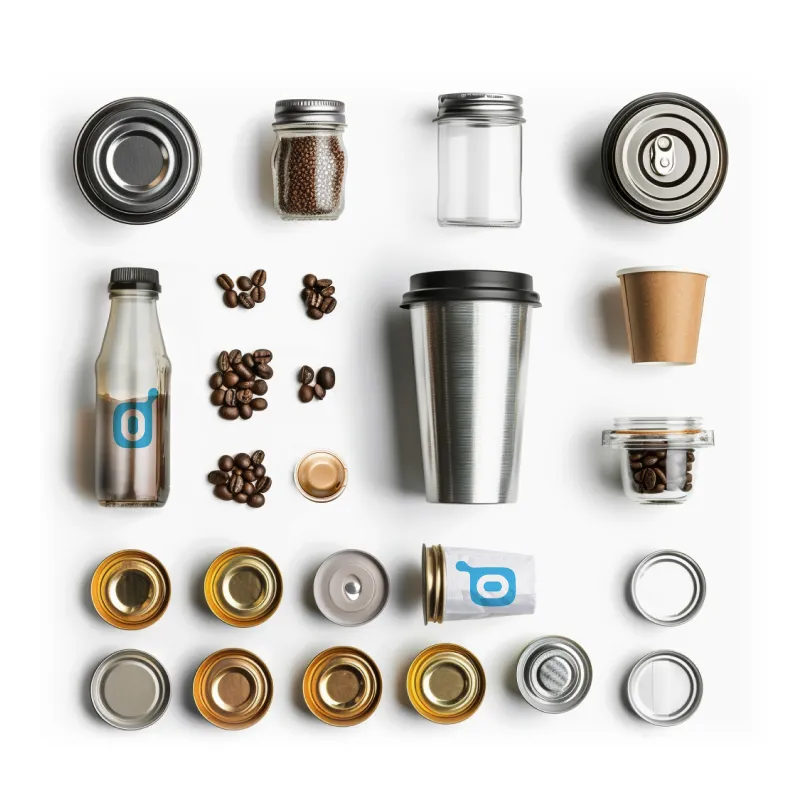
Testing Rigid Packaging For Leaks
At Oxipack, we specialize in delivering cutting-edge leak detection solutions tailored to rigid packaging formats. Our technology ensures that your products are securely sealed, safeguarding quality and customer satisfaction.
why Rigid packaging?
Rigid packaging offers robust protection for a variety of products, from pharmaceuticals and cosmetics to food items and industrial components. It’s essential for preserving the product's integrity, preventing contamination, and extending shelf life. Whether it's glass jars, metal cans, plastic containers, or cardboard boxes, ensuring airtight seals is crucial for maintaining product quality.
Oxipack’s solutions are expertly designed for precise sample testing, ensuring that each package tested meets stringent quality controls. Our technology is flexible, capable of testing a single can or multiple capsules simultaneously—depending on the rigid product's characteristics. For instance, in the case of coffee capsules, our system can test up to 16 pieces at once. This capability makes our equipment ideal for initial quality assurance assessments or routine checks, accommodating a range of sample sizes and types with ease.
Our machines possess the capability to identify even the minutest leaks, ensuring comprehensive quality control. This high sensitivity secures product safety and consumer trust by adhering to the strictest quality standards.
Our technology is engineered to accommodate a diverse range of rigid packaging sizes and shapes, from pharmaceutical vials to industrial containers, offering flexible solutions tailored to specific packaging needs.
Designed for efficiency, Oxipack's testing systems conduct rapid assessments to accommodate high-volume production environments, effectively preventing bottlenecks and facilitating continuous operation.
It generates a pressure difference of 700 mbar within thirty seconds, enabling the detection of leaks as small as 10 µm.
Incorporating advanced data capture and analysis, our systems provide real-time insights and detailed reports, aiding in quality tracking and decision-making processes for continuous improvement.
Oxipack's equipment adheres to the vacuum decay method standards set by ASTM F2338, providing a globally recognized assurance of quality and reliability in leak detection performance.
Designed with simplicity in mind, our leak testers indicate packaging status immediately: a green light for approved packages and a red light for those with detected leaks. This user-friendly interface facilitates quick decision-making and enhances operational efficiency.
The Importance of Non-Destructive Leak Testing for rigid Packaging
Rigid packaging benefits greatly from non-destructive leak testing. This method ensures the integrity and durability of containers while preserving their structure. It offers a reliable way to detect even the smallest of leaks, safeguarding contents and ensuring compliance with industry standards. Ultimately, non-destructive testing empowers manufacturers to enhance product reliability, minimize waste, and optimize operational costs.
Frequently Asked Questions
Actually almost all rigid-shaped packaging can be tested, such as trays, cups, capsules, cans, jars, containers, bottles, caps, vials, ampoules, etc.
What type of packaging would you like to test? From coffee capsules to large square blocks, we either have or we create a leak tester for your leak detection requirements. There are standard can and capsule sizes, but we supply custom made solutions for almost any product.
We have developed different leak testers for various types of packaging. All leak testers for rigid packaging test non-destructively using the vacuum decay method. The operation of the leak testers is simple, with a green light indicating that the packaging is sound (approved) and a red light indicating the presence of a leak. The leak testers also come with tailored molds that precisely fit the form of the rigid packaging, reducing the area to be measured and ensuring accurate testing.
For shape-retaining packaging such as trays, cups, and capsules, the Stationary Leak Tester XS or M is used to test for leaks. For cans, we use the Can Leak Tester, and for bottles, the Bottle Leak Tester. In the case of a milk powder manufacturer who wanted a leak tester for their tubs, the Tubs Leak Tester was developed. This is an example of how we are able to develop a leak tester for virtually any rigid-shaped packaging. Contact us to inquire about the possibilities at sales@oxipack.com.
Yes! Our engineers from the Projects Team will gladly help to make sure all requirements are met. Please discover the pharma industry.
Between 10 seconds (tubs tester) and less than 5 minutes (can leak tester), depending on the leak tester.
The lifetime of the membrane is about one year, depending on the frequency of use.
The data output of your leak tester is safe. All data will be stored on the tester itself for 365 days and can be extracted through USB or ethernet connection. Expansion packs are available like: OPC-UA, barcode scanner and printer.
Our Packaging Methods
Explore our other packaging methods.
Insights
Explore our latest News, Blogs, Cases and Whitepapers
Can my rigid packaging be tested?
Are you ready to make a lifelong impact in your business today? Stop wasting quality, time and money. Instead, choose Oxipack for detecting leaks in your packaging! Click below to request advice and see how our equipment can match your packaging specifications.
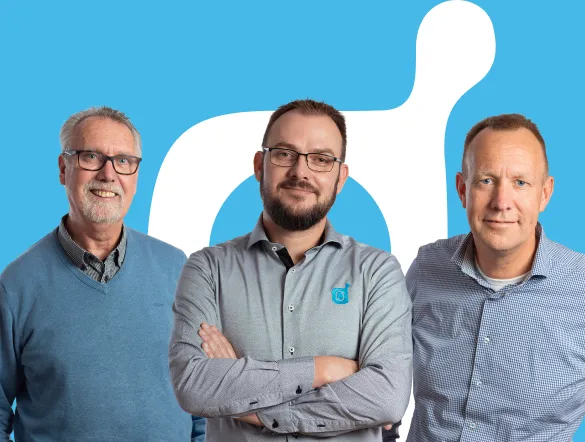