Ensuring Seal Integrity for Product Safety and Quality
Have you ever considered the impact a compromised package seal can have on product safety and quality? In industries like pharmaceuticals and food, maintaining the integrity of packaging seals is crucial to ensure products remain uncontaminated, safe, and effective throughout their shelf life. Seal integrity testing plays a vital role in this process, preventing leaks, spoilage, and contamination.
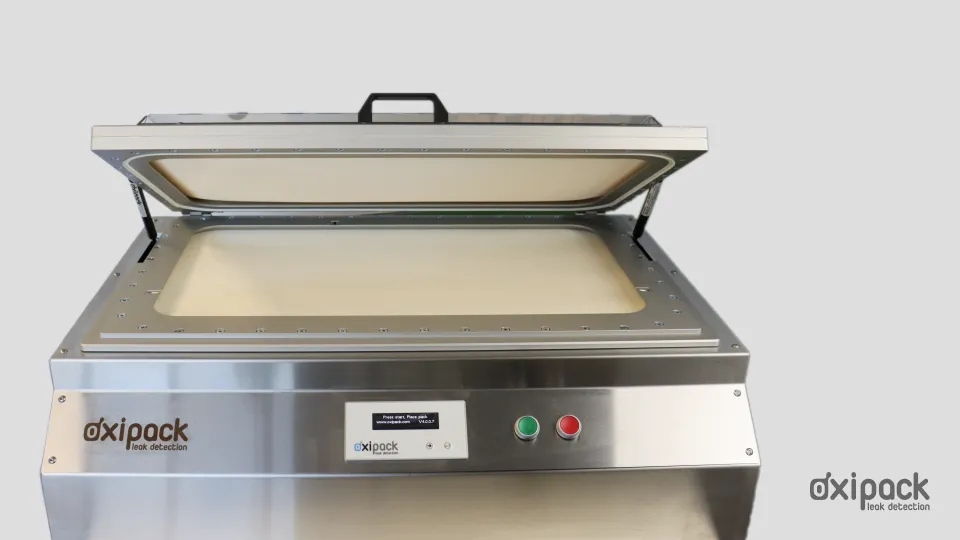
The Importance of Seal Integrity Testing
Seal integrity testing is an essential quality control measure in various industries, including pharmaceuticals and food. It ensures that packaging is correctly sealed and free from defects or leaks, maintaining product safety and quality.
Product Safety: A compromised seal can let air, moisture, and other contaminants enter the package, leading to spoilage, contamination, or degradation of the product. This not only affects the quality and efficacy of the product but also poses health risks to consumers.
Shelf Life: An intact seal extends the shelf life of products. For instance, food products exposed to air can spoil quickly. Ensuring seal integrity helps manufacturers extend the shelf life of their products.
Regulatory Compliance: Both the pharmaceutical and food industries must adhere to strict regulations and standards that mandate products meet specific quality and safety criteria. Seal integrity testing is often a regulatory requirement, and non-compliance can result in fines, product recalls, and reputational damage.
Cost Savings: Detecting seal defects early reduces the risk of product spoilage and waste, leading to significant cost savings and improved efficiency.
Customer Satisfaction: Consumers expect their products to be safe, fresh, and of high quality. By ensuring seal integrity, manufacturers can meet these expectations and build customer loyalty.
Seal Inspection Methods
Seal inspection is a critical component of package integrity testing. There are several methods for inspecting seals, including:
- Visual Inspection (ASTM F1886): This non-destructive test involves visually examining seals to identify potential issues such as gaps, wrinkles, or misalignments. While useful, it does not provide information about the strength or hermeticity of the seals.
- Dye Penetration Testing: A dye is applied to the outer surface of the package, and the package is pressurized. If there are any leaks, the dye will be drawn into the package, revealing the location of the leak.
- Bubble Leak Testing: The package is submerged in water, and air is introduced. Leaks are detected by observing bubbles. This method is destructive and makes the package unusable.
- Pressure Decay Testing: This method pressurizes the package and measures any pressure drop over time, indicating a leak. It is less sensitive to small leaks.
- Burst Testing: The package is subjected to increasing pressure until it bursts. This method assesses the package's strength but is destructive.
- Vacuum Decay Testing (ASTM F2338): At Oxipack, we utilize the vacuum decay method, a non-destructive technique that tests the seal and the rest of the package. This method is highly sensitive and suitable for various packaging types, including flexible pouches, sachets, containers, trays, cans, bottles, and caps.
Oxipack’s Seal Integrity Testing Solutions
At Oxipack, we offer a range of non-destructive seal integrity testing solutions designed to ensure product safety and quality. Our methods not only test the seals but also the entire packaging for leaks and defects, allowing approved packages to be returned to the production line without damage, thus saving costs and reducing waste.
Stationary Leak Tester (SLT): Our standard solution for pouch seal integrity testing, also providing information on the integrity of the entire package.
Stationary Leak Tester XS or M: Designed for testing rigid packaging, such as healthcare trays and flexible packages.
Can Leak Tester (CLT): Specifically for testing different types of cans.
Bottle Leak Tester (BLT): Ideal for testing the seal integrity of various bottle types.
Vacuum Leak Tester: Suitable for testing vacuum-sealed packages like coffee, rice, and yeast.
Seal integrity testing is a critical component of quality control in the pharmaceutical and food industries, ensuring product safety, regulatory compliance, and customer satisfaction. Oxipack's non-destructive leak detection solutions provide accurate and efficient testing for a wide range of packaging types. To learn more about our solutions and how quickly you can recoup the investment in our machines, we invite you to download our free white paper or contact us directly.