Operational Acceptance Testing (OAT) in the Packaging Industry
The Final Frontier of Packaging Quality
Imagine investing in state-of-the-art packaging machinery, only to discover that it fails under real-world conditions. This is where Operational Acceptance Testing (OAT) becomes crucial. In the packaging industry, OAT ensures that your packaging systems are not just theoretically sound but practically robust. It’s the final checkpoint before your products head to market, safeguarding against potential failures that could compromise product integrity and customer satisfaction.
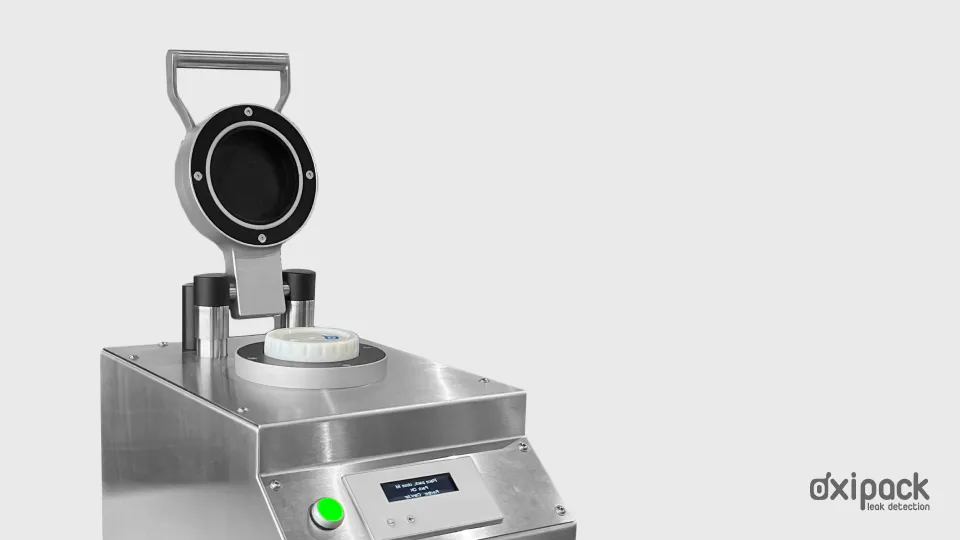
Understanding Operational Acceptance Testing (OAT)
Operational Acceptance Testing (OAT) in the packaging industry refers to the process of testing packaging systems or machines to ensure they meet the required standards for operational use in actual production environments. OAT is typically performed after the packaging system has passed all functional tests and is considered feature complete.
In the packaging industry, OAT involves testing the machine's ability to handle different types of packaging materials, its speed and accuracy, and its capacity to manage various production volumes. This includes verifying the functionality of both software and hardware components to ensure they operate as intended.
Key Components of OAT
1. Acceptance Criteria Definition:
The first step is defining the acceptance criteria or standards that the packaging system needs to meet. This includes the required levels of accuracy, reliability, and performance.
2. Planning and Preparation:
Set up the packaging system in a test environment that simulates real-world operating conditions. This involves preparing testing scenarios and creating a test plan that outlines the procedures and expected outcomes.
3. Functional Testing:
Functional testing ensures that the packaging system operates as intended. Each component and feature of the system is tested to verify correct functioning and adherence to performance standards.
4. Non-Functional Testing:
This step tests the system's ability to handle expected workloads and operate under various conditions. It includes high-volume production scenarios, different packaging materials, and error recovery.
5. Leak Detection Testing:
Leak detection testing ensures that the packaging maintains its integrity and prevents contamination or spoilage. Specialized non-destructive leak testing equipment, such as Oxipack’s vacuum decay method, is often used for this purpose.
6. Recording and Reporting Results:
Document any issues or defects found during testing. Provide a detailed summary of the testing procedures, results, and any corrective actions taken to improve system performance.
Importance of OAT in the Packaging Industry
Effective OAT ensures the reliability, safety, and efficiency of packaging systems, directly impacting product quality and customer satisfaction. It helps companies:
- Minimize the risk of product damage or failure during transportation and storage.
- Reduce the risk of costly recalls and reputational damage.
- Ensure compliance with relevant regulations and standards to avoid fines and penalties.
The Added Value of Leak Detection in OAT
Incorporating leak detection in OAT can identify leaks or defects in packaging before it reaches the market. This proactive approach allows manufacturers to address issues early, preventing larger problems such as product recalls or customer complaints. Oxipack’s non-destructive leak testing solutions, based on the vacuum decay method, are ideal for this purpose, providing accurate and reliable results.
Real-World Applications and Trends
With a growing trend towards sustainable and biodegradable packaging, such as paper-based materials, OAT is crucial. For example, in our case study on leak testing paper-based packaging, Oxipack’s solutions ensured leak-proof designs before market introduction. These advancements highlight the importance of OAT in developing robust packaging solutions across various industries, including food and beverage, pharmaceuticals, cosmetics, and electronics.
Ensuring Quality and Reliability
Operational Acceptance Testing is a critical step in ensuring that packaging systems are reliable, safe, and effective. By integrating thorough OAT procedures and advanced leak detection methods, manufacturers can safeguard product integrity and enhance customer satisfaction. For more information on how Oxipack’s solutions can add value to your OAT procedures, contact us directly.