What is Non-Destructive Leak Testing?
Have you ever wondered how the integrity of packaging is tested without causing damage? Non-destructive testing (NDT) is the answer. At Oxipack, we use NDT to ensure the quality of various packaging types without damaging them. This method is particularly beneficial for food packaging, pharmaceutical packaging, and cosmetic packaging, as it helps reduce waste and lower costs.
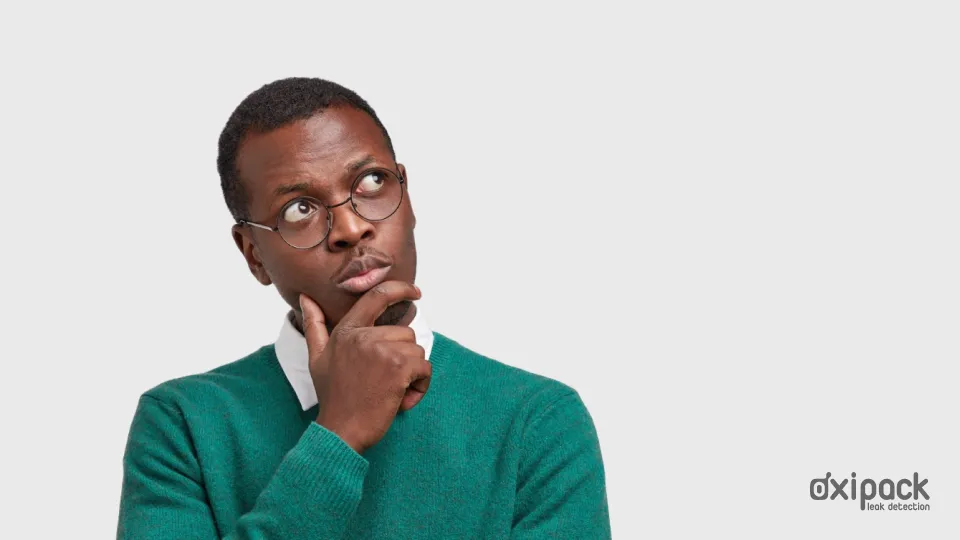
The Problem with Traditional Testing Methods
Traditional leak testing methods often result in significant waste, as perfectly good packages are discarded. Imagine the impact if 4-8 packages per hour, per production line, are wasted. This practice is not only costly but also environmentally unfriendly. Recognizing the need for a more sustainable approach, Oxipack offers a solution: non-destructive leak testing.
The Benefits of Non-Destructive Leak Testing
1. Preserves Product Integrity
With NDT, your products and packaging remain undamaged and dry. This means products that pass the test can continue through the production line without being destroyed.
2. Reduces Waste
Non-destructive testing significantly reduces waste within the production line, contributing to more sustainable manufacturing practices.
3. Lowers Rejection Rates
By ensuring the integrity of packaging early in the process, NDT reduces the likelihood of product rejection further down the production chain.
4. Eliminates Water Usage
Our NDT methods do not require water, making them more suitable for industrial environments.
5. Cost-Effective
An NDT machine can pay for itself in as little as a year, depending on various factors. Over time, this leads to lower overall costs.
6. Easy to Operate
Our machines are user-friendly, providing clear indicators: a green light for leak-tight packaging and a red light for detected leaks.
7. Accurate and Traceable Results
Oxipack’s NDT machines deliver precise and traceable measuring results, ensuring reliability and consistency.
8. Industrial-Grade Durability
Designed for industrial use, our machines feature robust construction, making them ideal for challenging environments.
Non-Destructive Leak Testing Methods at Oxipack
Vacuum Decay Method (ASTM F2338-09 Standard Test Method)
This method is suitable for both flexible and rigid packaging. It involves creating a vacuum around the package and monitoring for any changes in pressure that indicate a leak.
Vacuum Leak Tester for Dry Vacuum Packaging
This tester is ideal for dry vacuum packaging, such as coffee packs or yeast packaging. It uses a custom-made membrane to detect leaks without damaging the package.
Vacuum-Sealed Leak Tester
For products like vacuum-packed sausages or cheese, this tester uses an insert molded to the exact shape of the package. By creating a deep vacuum, it detects even the smallest leaks.
The NDT Process Explained
- Placing the Package: The package is placed in the chamber, the lid is closed, and the test is initiated.
- Creating a Vacuum: A deep vacuum is created by extracting all air between the membranes.
- Embracing the Package: The membranes embrace the package, protecting it from bursting and creating a very small measuring space.
- Detecting Leaks: In this small space, micro leaks are detected as air flows out of the package. Leaky packages are rejected.
- Equilibrium for Leak-Tight Packages: Leak-tight packages are undamaged due to the equilibrium created between the package and membranes, allowing them to return to the production line.
Non-destructive leak testing is a vital process for ensuring package integrity while reducing waste and costs. By adopting NDT, we move closer to a world without waste. Curious about how Oxipack can help you implement non-destructive leak testing solutions? Request advice today!