Ever wondered how secure the packaging of your favorite products really is? To guarantee safe, high-quality products that last, seals on packaging must remain unbroken. Seal strength testing is a key process in evaluating the reliability of these seals. In this blog post, we will explore the methods used for seal strength testing, compare them with seal integrity testing and vacuum decay testing, and highlight the advantages of using Oxipack's vacuum decay method for non-destructive leak detection.
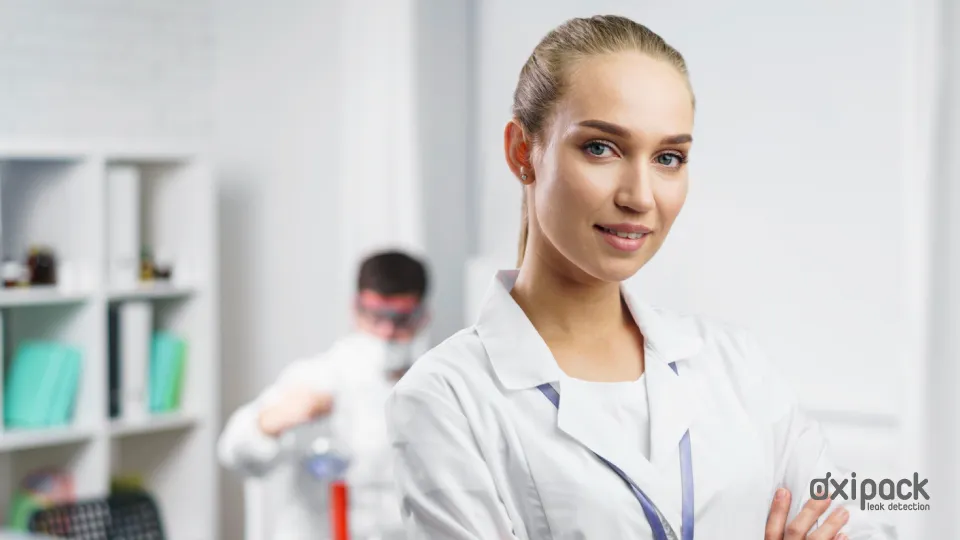
Understanding Seal Strength Testing
Seal strength testing evaluates the mechanical strength of seals in various packaging materials by measuring the force required to break or separate the sealed surfaces. This process is essential for ensuring that packaging can withstand the rigors of transportation and storage, preventing leaks and contamination.
ASTM F88: The Standard for Seal Strength Testing
The ASTM F88 standard is the most recognized method for seal strength testing. This destructive test involves securing the sealed area between two clamps and applying a controlled force until the seal breaks. The force required to break the seal is measured and recorded. This method is widely used for flexible barrier materials, including plastic films and aluminum foil, in industries like food and pharmaceutical packaging.
Heat Seal Strength Test Method
A specific variant of seal strength testing is the heat seal strength test. This method uses heated jaws to create seals between samples, assessing the quality and reliability of heat-sealed packaging. By evaluating factors such as temperature, pressure, and surface conditions, manufacturers can ensure their packaging can withstand the intended conditions.
Comparing Seal Strength Testing, Seal Integrity Testing, and Vacuum Decay Testing
Seal Strength Testing: Focuses on the mechanical strength of a seal by applying a force until the seal breaks. This method is destructive and only tests the strength of the seal.
Seal Integrity Testing: Evaluates if any leaks or breaches are present in the sealed package by applying a pressure differential and observing for leaks. This non-destructive method does not provide information on the strength of the seal but ensures the packaging's integrity.
Vacuum Decay Testing: Uses a vacuum to detect leaks in the entire package by monitoring pressure changes over time. This non-destructive method is highly sensitive and effective for various packaging types, ensuring the integrity of the whole package.
Combining Methods for Optimal Packaging Quality
Combining vacuum decay, seal integrity, and seal strength testing provides a comprehensive approach to packaging quality assurance. These methods together ensure that packaging not only has strong seals but also maintains overall integrity without leaks, offering optimal protection for products.
Why Choose Oxipack’s Vacuum Decay Method?
Oxipack’s vacuum decay method, compliant with ASTM F2338, offers a non-destructive, highly sensitive solution for leak detection in packaging. Unlike traditional methods like the bubble test or sniffer test, which are destructive and less precise, the vacuum decay method detects even the smallest leaks quickly and efficiently. This method is ideal for a wide range of industries, including food, pharmaceutical, and pet food packaging.
Seal strength testing is a vital process in ensuring packaging reliability. However, combining it with seal integrity and vacuum decay testing offers a holistic approach to packaging quality. Oxipack's non-destructive vacuum decay method stands out as a superior solution, providing accurate and efficient leak detection while maintaining the integrity of the packaging.
For more information about our methods and how to implement them in your production line, feel free to contact us. We're here to help you ensure your packaging meets the highest standards of quality and safety.