Oxipack's development team frequently receives inquiries from R&D managers, product developers, packaging technologists, and engineers who are looking to enhance their leak detection systems or to validate new packaging concepts.
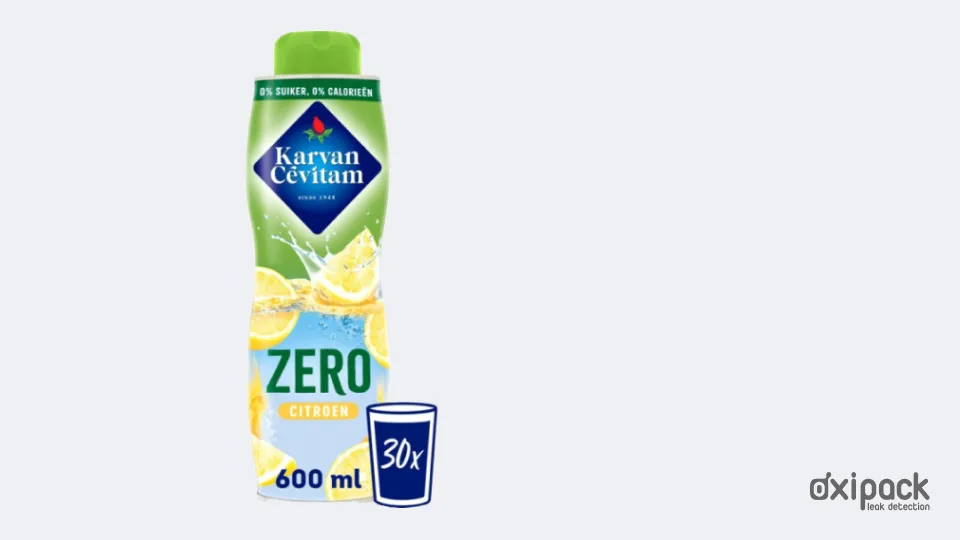
The Challenge of Detecting Cap Leaks
One recurring issue these professionals face is determining if a cap leaks, the exact extent of such a leak, its variability, and the potential impact on product shelf life. Traditional methods, such as the bubble test, lack the necessary precision, leaving these critical questions unanswered.
A Breakthrough in Leak Detection
A breakthrough occurred when an R&D team member approached Oxipack with a similar challenge. Impressed by our capability to detect minute pressure differences, they speculated whether we could also evaluate the integrity of pouring caps. Motivated by this inquiry, Oxipack quickly produced a prototype that successfully tested the caps for leaks.
Trial with Pouring Caps
Buoyed by this initial success, Oxipack's team adapted one of our standard leak testers for a trial involving 2,000 bottles with pouring caps. This test aimed not only to detect leaks but also to establish a new baseline for comparison with existing methods. The results from Oxipack's equipment provided precise insights into the quality directly attributable to the production process, eliminating any discrepancies caused by the testing equipment or method.
Confirmation and Validation
After several days of rigorous testing, it was confirmed that although the seals allowed a minimal amount of air ingress, they remained sufficiently airtight. Further validation came from microbiological tests, which showed that the current seal quality would not adversely affect the product's shelf life. Consequently, the company was able to continue with its existing packaging and manufacturing processes, confident that the airtightness of their products met all required standards.